1 发展背景
根据国家标准GB/T 22723-2008《天然气能量与测定》的规定[1],包含在单位体积(或单位质量)天然气中的能量可由式(1)来表示:
 |
(1) |
式中:E为能量,MJ;H为天然气的发热量,MJ/m3或MJ/kg;Q为天然气的量,m3或kg。
天然气能量计量技术问世20多年来,工业应用的能量测定技术只有两大类:气相色谱分析(间接测定)技术和热量计(直接测定)技术。这两类技术(尤其后者)的推广应用均涉及设备庞大、投资昂贵和维修困难等一系列技术经济问题,且都不能实现实时连续测定。故目前国内外大多仅在处理量达到120×104 m3/d以上的A级计量站使用基于气相色谱分析原理的间接测定技术,中、小型计量站一般都没有条件使用上述技术,通常以赋值技术来确定天然气能量[2]。
近年来,能量直接测定技术取得重大进展。美国San Antonio的西南研究院(SWRI)宣布已经研制成功一种可以利用关联法直接测定天然气能量的设备,要求输入的参数为超声流量计的声速、压力、温度和天然气中惰性气体(N2、CO2)的含量[2]。美国Houston的ITT仪表公司现已取得应用此项技术的许可证,并利用算法语言成功开发了新颖的天然气能量流量计专用软件包。2008年出版的美国天然气协会的AGA5号报告也介绍了此项新技术。但迄今尚未见工业应用的报导。
由于研制在管输(商品)天然气的高压下,直接测定天然气能量(发热量)的仪器是一项举世瞩目的科技难题,当前科研工作虽取得不少成果,但迄今仅有一例有关样机的报导[3],与工业应用尚有相当距离。然而,此类实时连续发热量测定仪的开发与应用,其重要性决非仅局限于降低能量计量的设备投资和操作成本,更有价值的是此类仪器的应用将有助于整体性地改善天然气输气网络的管理水平。其主要原因在于:
(1) 可以实时连续显示并记录不同时间周期中,输气管道内天然气的烃类组成(C1~C6+的摩尔分数)及其相应的体积基发热量,从而可以随时知道销售价格与实际气质的关系,为气质调配提供必要信息。
(2) 在提供发热量数据的同时,也显示并记录天然气的相对密度(ρ)和压缩因子(Z),从而为转换成作为计价基础的体积基发热量奠定基础。
(3) Z值计算仅与组分摩尔分数的测定误差有关,且由于是在管输压力下进行测定,不存在气相色谱仪测定时必然产生的“压降效应”,故就取样体积等产生的误差的环节而论,其测量不确定度应优于气相色谱技术。
(4) 能同时测定并记录(管输条件下的)水含量/水露点数据。
(5) 在实现(1)的前提下,同时也为商品天然气的沃泊指数计算及其相应的互换性管理提供了必要条件,这对我国正在大规模发展的输气网络具有意义。
(6) 若将上述一系列重要信息通过合适的通讯系统与已经建立的SCADA系统相连接,则可以大大提高天然气气质控制与能量计量系统的管理水平。
尽管当前开发此类仪器的技术路线甚多,但从基本原理分析大致可以归纳为3种类型:光谱式、声学式和核磁共振式。前两种类型的研究较多,但近年来有关核磁共振式的报导有所增加。下文以美国能源部资助的、由光谱科学公司(Spectral Sciences Inc. SSI)开发并已经取得专利的吸收光谱式发热量测定仪为代表进行介绍[4]。该仪器在操作压力超过6.8 MPa的条件下进行了全面的性能测试,并以高压管输商品天然气为样品气进行了现场(验证)试验[5]。
2 基本原理
分子吸收光谱是基于不同分子结构的物质对电磁辐射的选择性吸收而建立的分析方法。根据比尔-朗伯(Beer-Lambert)定律:当光线通过溶液时被测物质分子会吸收某一特定波长的单色光,而被吸收光的强度(A)与透射光通过的距离(L)及样品中吸光物质的浓度(c)成正比(参见式(2))。
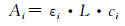 |
(2) |
式中:Ai为样品中被测组分i的吸光度;εi为被测组分i的(摩尔)消光系数;L为样品(吸光)池长度;ci为被测组分i的摩尔浓度。
当样品中含有n种不同的吸光物质(组分)时,样品的总吸光度(A)为各个组分吸光度的总和,可以通过式(3)求得:
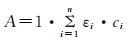 |
(3) |
当测定天然气中有关组分(i)的摩尔浓度后,根据GB/T 11062-1998《天然气发热量、密度、相对密度和沃泊指数的计算方法》的规定,天然气的体积基(标态)发热量(H)可以通过式(4)求得:
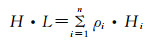 |
(4) |
式中:H为天然气的体积基(标态)发热量,MJ/m3;L为样品池长度,mm;ρi为被测组分i的相对密度;Hi为被测组分i(在燃烧参比条件下)的理想气体(标态)发热量,MJ/m3。
美国SSI公司开发的吸收光谱型传感器选择波长为900 nm左右的近可见光区,其主要原因在于:
(1) 根据局部模式理论(local mode theory),当波长变短时局部碳氢键(C-H)的特征(吸收)变得越来越明显;此时CH4、CH3、CH2和CH等功能团之间的区别则变得不甚明显。由于C1~C6+的各种分子均具有大致相同的吸光强度,故总发热量比按不同烃类组分分别测定后再加和的情况更精确,在典型测定条件下测量不确定度可以改善约0.1%。
(2) 当透射光的波长约为900 nm时,在分辨率为1~5 nm的条件下烃类组分吸光度随着其分子密度的增加几乎呈线性关系,故此类传感器基本上不需要进行现场标定。
(3) 近可见光区波长范围内的吸收光谱大致落在商品数码像机常用的标准硅CCD检测器的响应范围内,因而有利于使用廉价元件进行技术开发。
(4) 在波长900 nm左右区域进行的光透射,其吸光度远低于波长更长的可见光区域,故在3.4 MPa压力操作时约0.6 m长的吸光池即可达到最大的检测灵敏度,此操作条件适合对管输情况的天然气进行实时测定。
3 方法概述
如图 1所示,发热量测定仪安装在邻近孔板流量计和流量计算机附近。通过一根细小的取样管线,分流少量输气管道中的天然气至样品池,气体通过样品池后再返回输气管道;保持样品池的温度和压力与输气管道几乎相等;样品气在取样管线中压力降约0.7 kPa;气体在样品池中的停留时间为10 s。
样品气在样品池中的温度、压力及其吸收光谱均由合适的传感器发送至仪器的控制/监测(分析)系统。通常测得的发热量和压缩因子数据都发送至流量计算机,流量计算机在接收天然气的体积流量信息的同时计算并显示实时能量流量[5]。
图 2示出了发热量测定仪的组成元件及其功能。通过样品池后返回的透射光用光纤传输,形成的全息吸收光谱(图)用标准硅CCD检测器记录。通过样品池的气体样品中的CO2浓度用另一个辅助检测器测定。仪器内置的信号处理器记录CCD图像、温度、压力和CO2浓度等数据,并将CCD图像转换为吸收光谱图。然后,再将吸收光谱图解析为组分谱图,并根据各组分的拟合因子(fit coefficient)、测得的温度和压力,计算和显示各组分浓度、总(体积基)发热量和压缩因子。上述测量程序以20 s为一个周期重复进行。获得的“20 s数据”输入数据临时储存器,并以2 min为时间间隔进行记录。“小时平均”“日平均”数据也同时进行内部储存。
4 试验数据
试验用的标准气混合物(RGM)组成,其摩尔分数分别为:甲烷88.5%、乙烷5%、丙烷1%、正丁烷0.5%、异丁烷0.5%、二氧化碳2%和氮气2.5%。试验用样品池的长度为1.2 m、工况压力范围为0.85~6.7 MPa。以20 h为一个试验周期,测定了在不同操作压力下RGM的ρi(以标况条件下理想气体计)、工况条件下的体积基发热量(BTU/CF)和Z值(参见式(4))。本文为了区别标况发热量和工况发热量,标况发热量的单位以(BTU/SCF)表示,1 BTU/SCF = 37.3 kJ/m3。
获得的原始数据可以通过拟合而计算出标况条件下体积基发热量(BTU/SCF)和各组分的摩尔分数(Xi)。图 3所示即为上述组成RGM典型的吸收光谱图,以及据此拟合而得一系列组分的拟合吸收波长。图 3中的示例为在2.6 MPa压力下20 s周期的记录数据。为了更清楚地显示被测定的6种分子化合物的吸收峰,在图谱顶部的放大10倍的拟合数据基础上,再分别按5倍、20倍、40倍或80倍等倍数对图谱进行了放大。放大后数据清楚地反映出样品气中5种烃类组分和水分等6个组分的定量差别。
图 3中作为参比物(气体)的基础组分(组)由13种C1~C6同分异构体、水分和仪器的基线项构成。所有拟合而得的组分(相对)密度列于表 1,表 1中同时列出了按RGM组成计算而得的最佳估计值。确定最佳估计值时使用的Z值则按AGA8号报告规定方法计算。比较拟合值与计算值可以看出,所有被测组分的仪器测定数据与(理论)计算数据之间的相对误差不超过0.2%。
表 1
表 1 以标况理想气体计的各组分相对密度 (ρi)
Table 1 Relative density ρi at standard state of ideal gas
|
表 1 以标况理想气体计的各组分相对密度 (ρi)
Table 1 Relative density ρi at standard state of ideal gas
|
图 4示出了以2 min为时间间隔的6 h实时测定记录谱图,图 4中每个数据点对应于(图 3所示的)一个20 s测定周期。由于受样品池存在缓慢泄漏的影响,在6 h时间周期中图示数据的线性有所变差。将记录数据拟合为直线后,与按RGM组成计算值的相对误差为0.04%。
图 5示出了与图 4同一时间周期内拟合组分密度随时间的变化情况。图 5及表 1所示数据表明,两次测量之间拟合组分密度的波动范围小于总烃类密度(ρH)的0.1%。RGM组成中不存在的异戊烷组分在谱图上也有所显示,但对总烃类密度拟合值产生的相对误差仅为0.04%。
由于水分的吸光强度比烃类更强,因而水分测量的灵敏度也比烃类高得多。图 5所示的水分测定数据相当于样品气中水分的摩尔分数为(0.017±0.02)%,或质量浓度为(128±16)mg/m3。
5 Z值计算与转换
为了将测得的烃类组分密度转换为相应的摩尔分数,必须根据式(5)通过求解非理想气体状态方程以确定样品气中各组分的密度(ρi),然后进行加和而求得其在工况条件下的总密度(ρ)。
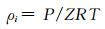 |
(5) |
式中: ρi为样品气中组分i的密度,kg/m3;P为工况压力,MPa;T为工况温度,℃;Z为工况条件下的压缩因子。
样品气总密度(ρ)是烃类气体密度(ρH)、水密度和惰性化合物密度之和。总密度和压缩因子(Z)可以根据详细的物料平衡数据用迭代法同时求得。对天然气混合物而言,Z值在1~0.85的范围随压力升高而下降的情况几乎与其组成无关。因此,状态方程的迭代过程很快收敛而解出Z值和惰性气体密度。然后根据分压定律,总密度可以根据各组分的摩尔分数由式(6)确定:
 |
(6) |
式中:Xi为样品气中组分i的摩尔分数,%;ρi为样品气中组分i的密度,kg/m3;ρ为样品气总密度,kg/m3。
求得天然气中各组分的摩尔分数后,其标况条件下的理想气体发热量(H)可以由式(7)计算:
 |
(7) |
式中:H为样品气(标况条件下)体积基发热量,BTU/SCF或MJ/m3;Hi为组分i(标况条件下)体积基发热量,BTU/SCF或MJ/m3;Xi为组分i的摩尔分数,%;T0为标况温度,℃;P0为标况压力,MPa;Z0为标况压缩因子。
当天然气的压力低于5.4 MPa且其中惰性气体摩尔分数不大于5%时,即使没有天然气中CO2含量的信息,Z值计算结果的不确定度仍可达到优于0.05%的水平。在SSI公司研制的发热量测定仪中同时设置了CO2辅助传感器,单独测定其在天然气中的含量,因而Z值计算结果的准确性更有所改善[5]。
图 6所示为根据图 4及图 5中数据计算而得的Z值,每个数据点代表一个20 s测定周期。图 6中的直线表示:将测得的温度和压力(波动)数据拟合为最佳结果后计算出的RGM的Z值。图 6中Z值数据的分散(性)是由于温度测量数据的波动所致。按图示数据估计,Z值的测量误差约为0.02%,从而导致重烃组分摩尔分数的测量误差达到0.2%。
图 7所示为以标况条件(BTU/SCF)表示测得的体积基发热量。仪器测得发热量的平均值为1 040.6×106 BTU/SCF(38.81 MJ/m3),比按RGM组成计算出的发热量高0.02%或0.2 BTU/SCF(0.008 MJ/m3)。在20 s测定周期数据点中,RGM样品气的测量误差为0.5%或0.5 BTU/SCF(0.02 MJ/m3), 此值略高于其计算值,原因在于温度和压力测量过程中进一步引入了误差。
6 测量不确定度分析
图 8和图 9分别示出了发热量测定仪的操作压力对样品气摩尔分数(Xi)和体积基发热量测量不确定度的影响。
图 8中标出了对应于每组测量数据的工况和标况发热量平均值随操作压力的变化情况,并与作为基准的(按RGM组成的)计算值(1 040.4×106 BTU/SCF或38.81 MJ/m3)进行了比较。图 8中的误差(柱)表示基于(测量仪表的)温度及压力读数的不确定度而导致的测量误差估计值。图示数据表明,16 ~20 h(较长)测定周期和1~6 h(较短)测定周期中全部测得的发热量平均值与相应的按RGM组成计算值之间的差值均不超过1 BTU/SCF(37.3 kJ/m3)。RGM中组分摩尔分数(Xi)计算的误差导致工况发热量计算产生的误差小于0.05%,但在压力低于5.8 MPa(850 psi)时,此项误差导致标况发热量计算产生的误差将达到0.6%(相当于0.6 BTU/SCF或22.4 kJ/m3)。
从图 9可以看出,标况发热量与工况发热量之间测量误差的差值随操作压力升高而增加,其原因在于RGM样品气中各组分含量(Xi)的测量误差随压力升高而增加。当操作压力达到1 000 psi(6.8 MPa)时,两者之间的差值达到1 BTU/SCF(37.3 kJ/m3);其原因在于在高压工况下,Z值计算对重烃组分摩尔分数的测量误差较敏感。例如在工况压力为1 000 psi(6.8 MPa)时,若正戊烷的测量误差为0.1%,将导致Z值计算的误差达到0.13%。但Z值计算误差并不影响管输条件下天然气工况发热量的测定,仅影响标况发热量测定。因此,如果仅需要测定管输条件下的天然气能量流率,就没有必要将工况发热量转换为标况发热量。
应该指出,Z值计算的误差仅与样品气中组分含量的测量误差有关,且此测量误差是包括了取样、测定等测量过程中的全部误差。与本文介绍的方法不同,目前工业上常用的气相色谱法是在常压或低压下测定的。由于“降压效应”将产生一系列系统误差,因而就Z值测定而言,在高压下取样和测定的吸收光谱法很可能比气相色谱法更准确,且方法的重复性也可能得到改善。当然,此可能性应进一步在现场试验中加以验证。
7 结论与建议
(1) 光学式实时测定热量计的研发代表了天然气组分含量分析的一个重要的技术开发方向。与目前天然气工业常用的以气相色谱法为基础的能量计量系统不同,光学式仪器是在管输(压力)条件下取样和测定,从而有可能排除气相色谱法系统存在的“降压效应”及其引入的一系列系统误差。
(2) 气相色谱仪一般不能测定天然气中的水分含量,且每个测定周期需要3~4 min;但光学式热量计不仅能在测定烃类含量的同时测定水分,作为连续记录式仪器实际每秒钟都在生成图像,且取样速率越高则测定的分辨率也越高。
(3) 从现有试验数据看,光学式热量计的准确度可以满足GB/T 18603-2001 《天然气计量系统技术要求》对A级站的要求(0.5%)。但根据国际法制计量组织(OIML)2007年发布的新版OMIL R140报告的规定,热量计法直接测定的准确度仍为0.5%,而气相色谱法间接测定发热量的准确度要求则改为0.6%。
(4) 相对而言,光学式热量计的设备投资及维护成本均较低,从而为在中、小型计量站中推广应用奠定基础。按GB/T 18603-2001的规定,一般在处理量超过120×104 m3/d的A级站才使用能量计量系统,规模较小的计量站则采用赋值的方法。据文献报导[5],光学式热量计有望在处理量超过28×104 m3/d的计量站中应用。
(5) 就当前的发展趋势来看,发热量(实时)直接测定仪的应用不仅能解决能量计量系统的准确度和连续性,也能发送整个输气网络的管理水平,故此类热量计的技术开发受到普遍重视。但很可能存在分光光度法仪器常见的测量数据漂移等问题,故迄今尚未见工业应用的报导。
[1] |
常宏岗, 罗勤, 陈赓良, 等. 天然气气质管理与能量计量[M]. 北京: 石油工业出版社, 2008.
|
[2] |
黄黎明, 陈赓良, 张福元, 等. 天然气能量计量理论与实践[M]. 北京: 石油工业出版社, 2010.
|
[3] |
A. Sivaraman, et al. . Development and deployment of an acoustic resonance technology for energy content measurements[C]. 23rd World Gas Conference, Amsterdam, 2006.
|
[4] |
S. Adler-Golden, et al. . US 805822058[S]. 1998. 10. 13.
|
[5] |
N. Goldstain, et al. . Real time optical BTU measurement of natural gas at line pressure[C]. 4th International Symposium on Fluid Flow Measurement, Dever, Colorado USA, 1999.
|